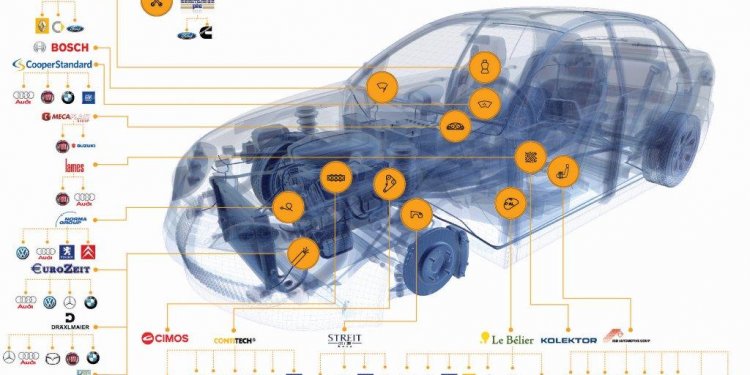
Automotive industry ratios
Carbon-fiber composites (also called carbon-fiber reinforced plastics or CFRP) are finding their way into new applications as industries demand materials with ever-higher strength-to-weight ratios, corrosion resistance, and workability. Over the past 60 years, CFRPs have been increasingly used to replace metal in applications where light weight has outsized value (capable of supporting prices that can reach $140/lb), primarily for reducing fuel consumption.
CFRPs face a divided course: more successful in high-value areas particularly sporting goods, aerospace, armed forces, and supercars, but listed out of most large-volume areas, especially the mainstream automotive companies. This can carry on until rising methods and materials increase CRFP manufacturing and lower the large costs.
In 2020, CFRPs across all applications will include a $35 billion market, including $6 billion in automotive CFRPs, relating to Lux Research. However, that automotive use may be restricted to deluxe and race automobiles. Analyses indicate that large-scale, mainstream CFRP automotive use before 2020 is not likely. But sometime after 2020, the possibility level of CRFP found in cars and trucks could dwarf all the applications, possibly reaching hundreds of vast amounts of bucks.
Because of this, most major automotive organizations and carbon-fiber manufacturers are developing partnerships, joining consortia, and performing study to carry automotive CFRPs closer to commercial reality. Oak Ridge nationwide Laboratory’s (ORNL) Carbon Fiber Composites Consortium remains the many connected entity from the automotive partnership map, with 23 OEM, Tier 1, and major material provider partners. ORNL’s Carbon Fiber Technology Facility, a 25-ton/yr. pilot carbon-fiber production range is checking out methods of making dietary fiber at lower expenses. The facility demonstrated couple of years ago that it can turn-out standard modulus carbon fibers—with tensile strengths of 500 ksi and modulus as high as 36 Msi—using textile-grade polyacrylonitrile (PAN) predecessor. ORNL states it costs under half as much as fiber-grade PAN.
Today, ORNL deals with competitors from Carbon Nexusan’s 20 ton/yr. pilot production range founded by Australia’s Victorian Centre of Advanced components Manufacturing. Carbon Nexusan, integrating with Dow, Quickstep, Volkswagen, and Australian national research agency CSIRO, is developing its very own option precursor, tensile energy improvements, and energy-efficient technologies, many of which could possibly be combined with ORNL’s practices. Along with advances in dietary fiber manufacturing, suppliers throughout the value sequence tend to be building quicker, more effective equipment, resins created for automotive CFRP use, and scalable CFRP recycling methods.
Among auto companies, BMW stands apart as a pioneer of CFRP use. It first invested in carbon-fiber maker SGL in 2009, a relationship that continues with BMW trading $200 million more just last year to press production capability from 6, 000 tons to 9, 000 tons/yr. BMW will use the materials with its i-Series electric and plug-in crossbreed vehicles, that are presently moving off production outlines at a level of 100 automobiles a day.
More recently, BMW features partnered with Boeing, a world leader in using CFRPs for aerospace manufacturing. The two aspire to improve CFRP manufacturing and recycling. By using both upstream fibre ability financial investment and the familiarity with experienced people like Boeing, BMW is positioning itself to lead the way in large-scale automotive CFRP manufacturing.