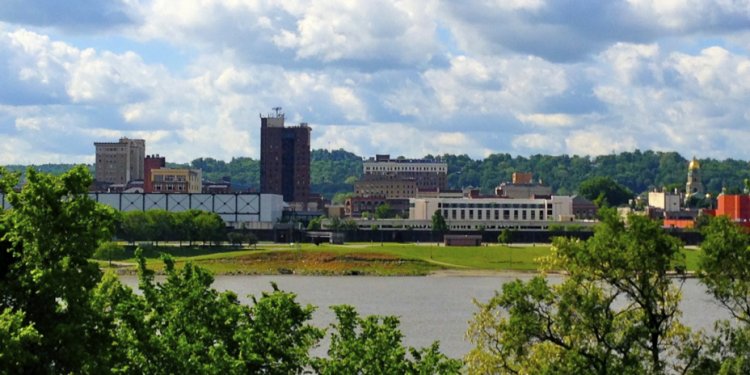
Car wheel Manufacturing
Below are a few notes on aluminum car wheels that individuals assembled a couple of years ago included in a college task. These notes give some insight into the history, manufacturing procedures, products and design considerations regarding car rims.
Reputation for aluminium car rims
The first light-alloy sheet aluminium vehicle tires were used in Daimler-Benz and Auto-Union racing automobiles into the 1930s. Inside 1960s, Porsche started the batch production of sheet tires, which contained a wheel rim and nave. The initial high-volume creation of sheet rims in European countries were only available in 1979 for Daimler-Benz cars destined the American.
Through additional development of manufacturing process for wheel wheels and naves, the manufacturing costs had been reduced markedly to ensure an aluminum sheet wheel has been stated in large numbers when it comes to BMW 5 Series since 1995
Using aluminium rims on passenger vehicles began aided by the upper-class or flagships models to be able to give them a unique personal touch.
Primarily cast at the moment, they started in the 1970s is factory-fitted to mass-produced vehicles.
Rims are now actually representing about 15percent associated with the average aluminum content in passenger vehicles and light vehicles, incase the key motivation was styling with primarily cast solutions, fat loss demands have actually resulted in development of even more technical cast but in addition forged and fabricated solutions.
These components have, but vital protection features and must fulfill large requirements of design, manufacturing and workmanship.
Design/material selection considerations
Tightness
Structural rigidity (design centered) is the standard price to consider when designing an aluminum wheel to quickly attain at least equivalent vehicle behavior just like an equivalent metallic wheel.but product tightness (Young’s modulus) is extremely small dependent on alloy and temper.
Static behaviour
Yield strength is known as in order to avoid deformation under maximum axial attempts (accelerations and stopping) and radial people (plus turning). Misuse instances are considered pertaining to tensile energy. Yield tests under pressure may also be conducted to check on this behavior.
Fatigue behavior
This is the most important parameter for dimensioning. Finite factor software is methodically utilized during design. Provider stresses are believed, including multi-axial stresses since recently. Rotary flexing and rim moving examinations are used to validate these computations.
Crash worthiness
Mainly, but not just, linked to stress/strain curves in huge displacements. Crashworthiness is beginning to be now simulated. However impact examinations systematically check out the opposition to accidental collisions like pavements impacts.
Air Conditioning
No matter what sort of wheel (cast, forged, strip, combined wrought-cast, …), aluminum dissipates heat more quickly than metal. Further, aluminium tires behave as an extremely efficient heat sink. This results in considerable improvements of braking effectiveness, and a diminished threat of tyre overheating.
Style – body weight conserving
Reduced total of weight associated with the unsprung mass of cars is a key concern. A compromise has to be accepted if styling requirements determine various manufacturing technologies (s. figure).
Dimensional
An ideal mass stability is an integral parameter to prevent considerable oscillations. As a result, cast and forged tires tend to be machined. Lightness in addition decreases vibrations of aluminium sheet wheels
Deterioration
Cast and forged tires tend to be coated or lacquered after substance transformation. Strip tires are polished and varnished or in addition painted. Even within uncoated iron/aluminium disk, or hub screen, no significant corrosion has actually ever before been seen for just about any